성능·출력 등 결정
'게임 체인저' 떠오른 건식 공정
제조 비용 최대 30% 절감
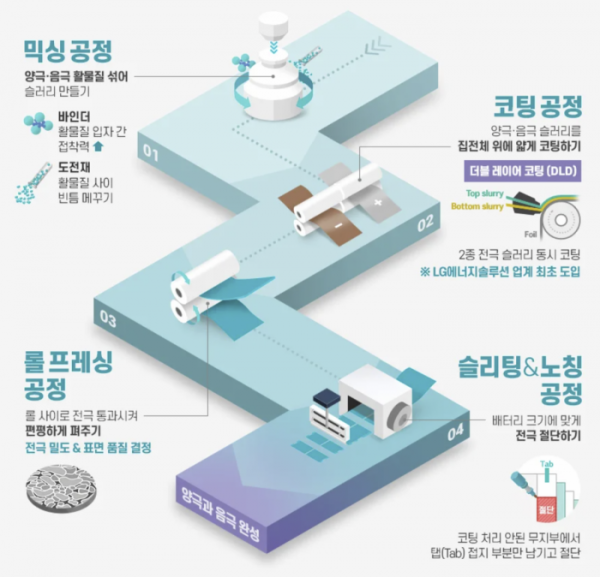
전기차에 들어가는 리튬이온 배터리는 크게 전극 공정→조립 공정→활성화 공정→팩 공정 등 4단계로 나뉜다.
배터리 제조의 핵심 단계이자 첫 과정인 전극(극판) 공정은 리튬, 니켈, 코발트 등으로 이뤄진 활물질을 집전체에 코팅해 양극과 음극을 만들고 필요한 크기로 절단하는 공정이다. 이 과정에서 배터리의 성능이 결정된다.
우선 양·음극 활물질과 접착력을 높이는 바인더, 전자 이동을 담당하는 도전재, 유기용매 등을 혼합해 액체 상태인 슬러리를 만든다. 슬러리로 만드는 이유는 집전체에 균일하게 도포하기 위해서다.
양극 슬러리는 알루미늄박에, 음극 슬러리는 동박 양면에 코팅한 후 100도 이상의 오븐에서 건조해 슬러리 내 용매와 수분을 제거한다. 건조 공정에서 발생하는 가스도 배출시킨다.
그다음 두 개의 롤 사이로 전극을 통과시켜 편평하게 펴주는 ‘롤 프레싱(압연)’ 과정을 거친다. 전극 표면과 활물질의 결합력을 높이고, 리튬이온을 원활히 이동할 수 있게 한다. 즉 전극이 납작해질수록 배터리의 에너지 밀도가 향상된다.
납작해진 전극들을 일정한 폭으로 재단하는 슬리팅 공정과, 전극을 가로로 잘라 ‘브이(V)’자 홈과 양극·음극 탭(Tab)을 만드는 노칭 공정을 마치면 전극 공정이 완료된다.
대부분의 배터리 기업은 액체 상태인 슬러리를 극판에 코팅하고, 유기용매를 건조하는 ‘습식 공정’을 적용하고 있다. 그러나 건조 과정에 상당한 비용이 투입되는 단점이 있다.
또 에너지 밀도를 높이기 위해 슬러리를 두껍게 코팅할 경우 소재가 균일하게 붙어있지 못하고 이동하는 ‘마이그레이션(Migration)’ 현상이 나타날 수 있다.
최근 배터리 업계는 양·음극 활물질과 도전재, 바인더를 용매 없이 혼합해 고체 파우더로 만드는 ‘건식 공정’ 기술 개발에 뛰어들고 있다.
건식 공정은 건조 과정에 들어가는 설비와 비용을 줄여 습식 공정 대비 전극 제조 비용을 17~30% 낮출 수 있다. 또한 전극에 활물질을 두껍게 코팅해 에너지 밀도를 높일 수 있다.
건식 공정은 2020년 테슬라가 도입하겠다고 밝힌 지 4년이 지난 현재까지도 상용화되지 못할 정도로 기술적 난도가 높다. 액체를 균일하게 바르는 것보다 고체 파우더를 고르게 도포하는 것이 어렵기 때문이다.
테슬라는 7월 건식 양극으로 생산한 배터리를 탑재한 사이버트럭을 테스트 중이고, 4분기에는 제품을 출시할 계획이라고 밝혔다.
국내 기업 중에선 LG에너지솔루션이 4분기 충북 오창에 파일럿(시범생산) 라인을 구축할 계획이고, 2028년을 상용화 목표 시점으로 제시했다. 삼성SDI도 최근 충남 천안에 ‘드라이 EV’라는 이름의 파일럿 라인을 완공한 것으로 알려졌다.