한화케미칼
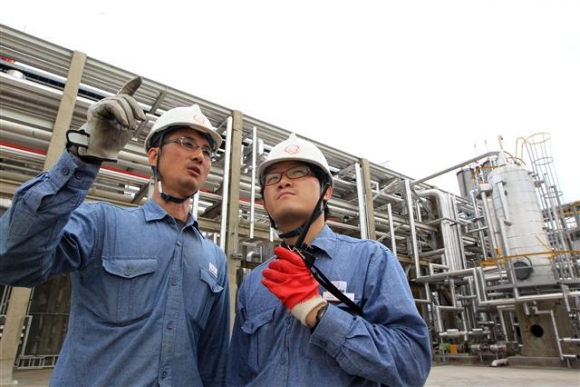
지난달 18일 울산의 진미(珍味)를 느끼게 해 주겠다며 한 식당에 데려간 한화케미칼 직원이 건넨 말이다. 식사 자리에서 반주를 곁들인 인사 치레 정도로 생각했다. 한화케미칼 울산1공장을 찾기 전의 일이다. ‘소주 한 잔’에 숨은 뜻이 있었다는 것도 모른 채….
울산에서만 맛 볼 수 있다는 ‘아귀수육’을 뚝딱 해치운 뒤 울산 시가지를 관류하는 태화강을 따라 25분 남짓 차를 타고 달렸다. 전날 태풍 ‘산바’가 많은 비를 뿌리고 간 탓인지 태화강은 황색을 띠었다.
두 번의 경비초소를 지나 도착한 곳은 울산석유화학단지 내에 위치한 한화케미칼 EVA(에틸렌비닐아세테이트) 공장.
시큼한 냄새가 코를 찔렀다. 양미간에 힘이 잔뜩 들어갔다. “그러게 소주 한잔 하셔야 한다니까요. 후각을 마비시켜야 해요”(웃음). ‘소주 한 잔’에 담긴 의미를 그제야 이해했다.
안내를 맡은 박구동 상무(울산1사업장 담당)도 “주변 석유화학단지에서 많이 사용하는 솔벤트(Solvent)와 에틸렌(ethylene) 냄새인데 조금 불편하겠지만 인체에는 무해하다”고 안심시켰다.
한화케미칼 울산1공장은 1984년 국내 최초로 EVA를 생산했다. 현재 26만㎡(7만8600평) 부지에 연산 16만톤 규모의 EVA 생산시설을 갖추고 있다.
안전모, 안내마이크와 연결된 이어폰을 착용하고 최근 상업 가동한 4만톤의 증설라인 앞에 섰다. 굉음과 함께 컨테이너박스 보다 약간 작은 초고압 압축기(compressor)가 눈에 들어온다. 바로 옆에 있는 사람에게 힘껏 소리 질러야 겨우 알아들을 수 있을 정도로 심한 소음이 지속된다.
박 상무는 “원료를 최대 2400기압까지 고온·고압으로 처리하는 세 번의 핵심공정을 거치기 때문에 열교환기와 압축기에서 발생하는 기계음이 매우 크다”면서 “압축된 가래떡 모양의 EVA를 잘 개 썰어내는 가공공정을 거쳐 최종 제품이 나오게 된다”고 설명했다.
파이프라인으로 연결된 EVA의 이동로를 따라 바로 옆 공장으로 발길을 옮겼다. 최종 제품인 투명한 EVA 알갱이들이 쏟아지고 있었다. 흡사 방앗간의 정미기에서 떨어지는 쌀알을 연상시켰다. 원료를 집어넣은 후 여기까지 걸리는 시간은 단 30초에 불과하다.
이렇게 만들어진 EVA는 자동(25kg) 및 수동(500kg) 포장공정을 거쳐 1만8000개의 파렛트(pallet)를 보관할 수 있는 자재창고로 옮겨진다. 파렛트 한 개에는 25kg짜리 EVA 20~30포대를 쌓는다.
EVA는 투명성, 접착성, 유연성 등이 우수해 발포용(신발 밑창), 코팅용, 전선용, 핫멜트(접착제), 태양전지용 시트 등 다양한 용도로 사용된다. VAM(비닐아세테이트 단량체)의 함량에 따라 저함량과 고함량으로 구분되는데, VAM 함량이 22%~40% 정도인 제품을 고함량 EVA라 하며 부가가치가 높아 특화제품이라고 한다. 주로 코팅, 태양전지용 시트, 핫멜트(접착제)의 원료로 사용된다. 이번에 증설한 플랜트는 고함량 EVA를 주로 생산한다.
한화케미칼은 고부가 특화제품의 생산 확대를 통해 경쟁력을 강화할 계획이다. 글로벌 경기침체로 인한 수요 감소와 에틸렌 가격 상승 등 최근 석유화학업계가 처한 위기를 극복하기 위해서다.
박 상무는 “화학수지 범용 제품 생산은 일본 등 선진국이 특화제품에 집중하면서 우리나라로 넘어온 것이고, 이제는 한국에서 원가 경쟁력이 있는 중동지역으로 넘어가고 있다”며 “국내 산업 경쟁력 향상을 위해서도 특화제품의 비중을 늘리고 더 많은 부가가치를 창출해야 한다”고 강조했다.