올해 현대기아차 중국 모델부터 적용… 향후 미국ㆍ유럽차로 확대
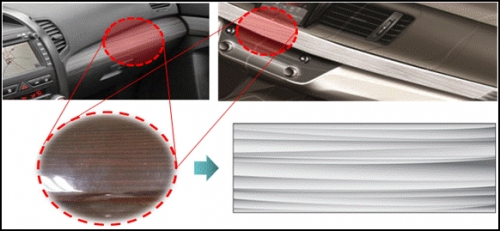
삼성SDI는 지난 24일 ‘2015년 신기술 인증서 수여식’에서 현대자동차, 현대모비스, 우성정공과 공동 개발한 ‘3차원 입체패턴 구현 이중사출 성형기술’로 신기술(NET) 인증을 획득했다고 30일 밝혔다.
산업통상자원부와 국가기술표준원이 주관하는 신기술 인증은 국내 최초로 개발한 기술 및 기존 기술을 혁신적으로 개선한 성과를 신기술로 인증해 주는 국가인증 제도다.
이번에 인증받은 신기술은 자동차 대시보드에 장착되는 가니시 소재의 질감을 3차원 입체패턴으로 구현한 기술이다. 삼성SDI가 기아자동차 디자인센터, 현대자동차 재료개발센터, 현대모비스, 우성정공과 함께 업계 최초로 개발에 성공했다. 통상 우드, 메탈, 인서트 필름, 도장 등의 방식으로만 제작돼 왔던 가니쉬에 플라스틱 소재를 적용했고 플라스틱으로만 표현할 수 있는 3차원 입체패턴의 이중사출 공법을 사용했다는 데 의미가 있다.
최근 자동차 선택 기준으로 감성 디자인이 중시되면서 기존 플라스틱에 특수공정을 더해 인테리어 소재의 고급스러운 느낌을 살리려는 업계의 경쟁이 치열해지고 있다. 이로 인해 새로운 디자인 개발을 위해 디자인, 소재, 개발, 금형, 사출 등 일련의 과정이 모두 중요해지고 있는 상황. 이번 3차원 입체패턴 개발도 각 과정의 핵심 참여자들이 지속적으로 협업한 끝에 3년이라는 긴 시간을 거쳐 성공한 사례다.
개발 작업은 바로 보르도 TV에서 시작됐다. 보르도 TV의 이중사출에서 영감을 얻은 현대자동차 재료개발센터가 자동차용 이중사출 금형 개발에 투자를 시작했고 기아자동차의 디자인센터와 삼성SDI의 개발팀이 새로운 컬러와 물성 개발에 협업해 전에 없던 새로운 디자인과 소재를 구현해 낸 것.
보르도TV에는 빨간색 소재 위에 투명 소재를 이중으로 사출해 와인잔을 표현했다면 이번 3차원 입체패턴은 메탈릭 소재(ABS)와 폴리카보네이트를 이중으로 사출성형해 개발됐다.
입체패턴 이중사출 기술 상용화에 성공함으로써 자동차 제조사 입장에서는 외관 효과를 위한 3단계 표면처리의 공정을 1단계로 줄여 원가절감과 생산성 증대 효과를 거두게 됐다. 특히 이번 기술은 도장공정을 없애 환경오염을 막고 휘발성 유기화합물의 발생을 억제해 새차 증후군을 크게 줄인 친환경 기술로도 인정받고 있다.
3차원 입체패턴 내장재는 현대·기아자동차의 중국 시장 전용 모델에 올해 처음 채택될 예정이다. 세계 최대 자동차 시장인 중국 출시 모델에 적용된 만큼 향후 매출 확대를 위한 유리한 고지를 선점했다는 평가다.
삼성SDI 케미칼사업부 응용기술그룹 정재엽 대리는 “이 기술이 적용될 현대기아차의 신규 모델 생산규모는 2017년까지 국내 44만대, 해외 21만대 규모가 될 전망”이라며 “앞으로 기술 차별화를 통해 적용 시장을 확대해 나갈 계획”이라고 말했다.
삼성SDI는 향후 이 소재의 적용 범위를 도어 가니시, 리어 램프, 아웃 사이드 미러 등 플라스틱 소재가 적용되는 다양한 부분으로 확대할 계획이다. 아울러 중국 시장에 이어 자동차 본고장인 미국, 유럽 시장에 출시되는 새로운 모델에도 적용을 추진할 방침이다.
이미 삼성SDI는 케미칼사업의 성장동력으로 고부가 자동차 소재를 앞세워 글로벌 시장 확대에 나서고 있다. 이번 신기술 인증에 바탕이 된 무도장 메탈릭 소재는 올해 글로벌 시장에 출시된 포드의 주력 모델인 2015년형 몬데오 센터페시아에 장착됐다.
삼성SDI는 앞으로도 완성차의 감성품질을 좌우하는 고부가 소재 개발에 역량을 집중해 글로벌 시장을 개척하고 자동차 업계의 친환경·디자인 중시 트렌드에 발맞춰 차세대 엔지니어링 플라스틱 제품 라인업을 확대해 나갈 계획이다.
삼성SDI 케미칼사업부 자동차사업팀장 정용태 상무는 “IT용 소재의 노하우를 접목해 개발한 제품들이 서서히 시장에서 두각을 나타내고 있다”며 “이런 기술과 경험을 자동차 소재 시장에서 차별화 포인트로 활용해 경쟁력을 확보해 나갈 계획”이라고 말했다.