밴드 커팅 등 고위험 작업 대체
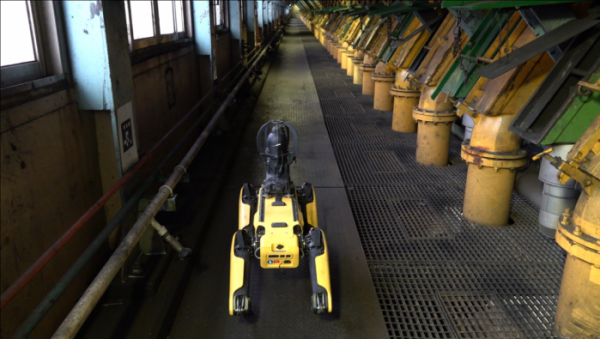
철강업계가 로봇ㆍ인공지능(AI) 도입에 한창이다. 업무 효율성을 향상시켜 경쟁력을 강화하는 동시에 안전 관리에 만전을 기한다는 복안이다.
23일 철강업계에 따르면 포스코, 현대제철, 동국제강 등 철강사들은 ‘스마트팩토리’ 구축에 한창이다. 빅데이터와 첨단 정보기술(IT)을 공정에 적용해 AI 기반의 지능형 공장으로 전환하고 있다.
‘맏형’ 포스코는 현장에서 설비 점검에 힘쓰는 직원의 안전 리스크를 제거하는 것은 물론, 업무 생산성을 높이고자 로봇 하드웨어, 제어 소프트웨어, 스마트 센서와 AI 기술 등을 통합하는 4대 로봇 솔루션(고정형ㆍ이동형ㆍ원격운전ㆍ플랫폼 솔루션)을 개발하고 있다.
4족 보행 로봇솔루션은 기존 바퀴형 이동 로봇과 비교하면 턱이나 계단 같은 장애물에 제약을 덜 받고 움직임이 자유롭다. 현재 광양제철소 1고로 풍구상에서 사람을 대신해 임무를 수행하고 있다. 포항제철소에는 높은 온도로 인해 작업자가 직접 점검하기 어려운 5기 코크스 오븐을 자율운전 통합관제 플랫폼(PosRX Platform) 기술을 활용하고 있다.
포스코DX는 산업현장의 사고 위험이 큰 업무를 로봇이 대신하는 인텔리전트 팩토리 구현에 나섰다.
포스코DX는 포항제철소 냉연 공정의 밴드 커터(Band Cutter) 자동화를 추진했다. 압연 공정에서 생산한 제품인 코일이 풀리지 않게 밴드로 묶어 두루마리 휴지 형태로 각 공장으로 출하되는데 이를 재가공하려면 밴드를 제거해야 한다. 제거 과정에서 작업자가 다칠 수 있어 로봇이 대신하게 했다.
동국제강그룹은 2018년 스마트팩토리 구축을 위한 별도 위원회를 설립하고 제조 현장의 혁신을 추진하고 있다.
최근 동국씨엠 부산공장은 스마트 물류 시스템 도입에 집중하고 있다. 이 스마트 물류 프로젝트의 핵심은 △자동 포장 설비 △자동 운송 설비 △자동 무인 크레인 시스템이다.
자동 포장 설비(Auto Packing Line)는 기존에 수작업으로 이뤄지던 코일 포장 과정을 자동화해 시간당 최대 20개의 포장이 가능하다. 이를 통해 부산 공장 전체 제품 포장량의 45%를 처리하고 있으며, 다양한 품종의 소량 생산에도 대응할 수 있도록 설비를 구성했다.
자동 운송 설비(Automated Guided Vehicle)는 코일을 안전하게 운반하는 자율주행 시스템으로 총 4대 도입했다. 이 설비는 75톤(t)의 운송 능력을 갖췄으며 국내에서 유일하게 옥외 도로에서 중량물을 운송할 수 있다. 또한, 동국씨엠은 올해 기존의 수동 전동차(100톤)를 무인 전동차(Rail Guided Vehicle)로 전환하는 방안도 검토하고 있다.
무인 자동 크레인은 건물 천장에 설치해 중량물을 자동으로 들어 올려 지정된 위치에 내려놓는 설비다. 총 10대를 도입함으로써 작업 시간을 줄이고 안전사고를 예방할 수 있게 됐다.
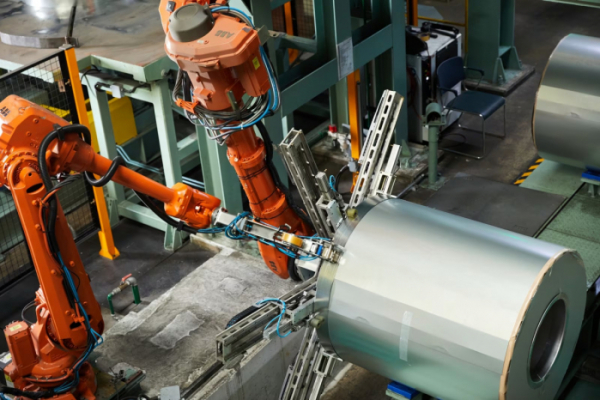
현대제철은 글로벌 판매기반 구축을 위한 업무협약(MOU)을 비롯해 설비 신규 투자를 통해 고부가가치 제품 양산체제에 속도를 내고 있다.
현대제철은 최근 체코의 최대 자동차 부품사 중 하나인 타웨스코(TAWESCO)와 이탈리아의 자동차 강판 전문 가공 업체(SSC)인 유사이드(EUSIDER)와 탄소 저감 강판 판매를 위한 MOU를 체결했다. 고객사와 함께 탄소 저감 강판 부품테스트를 진행하는 한편, 탄소 저감 강판에 대한 공동 마케팅을 추진한다.
싱가포르 과학기술청 산하 연구센터인 ARTC(Advanced Remanufacturing and Technology Center)와 함께 비전 인공지능(Vision AI) 기술개발 협력을 추진한다. 이번 협력을 통해 현대제철은 제품 표면 결함 파악 등에 적용 가능한 AI 모델을 개발함으로써 철강 제조공정의 혁신을 이뤄낼 것으로 기대하고 있다.